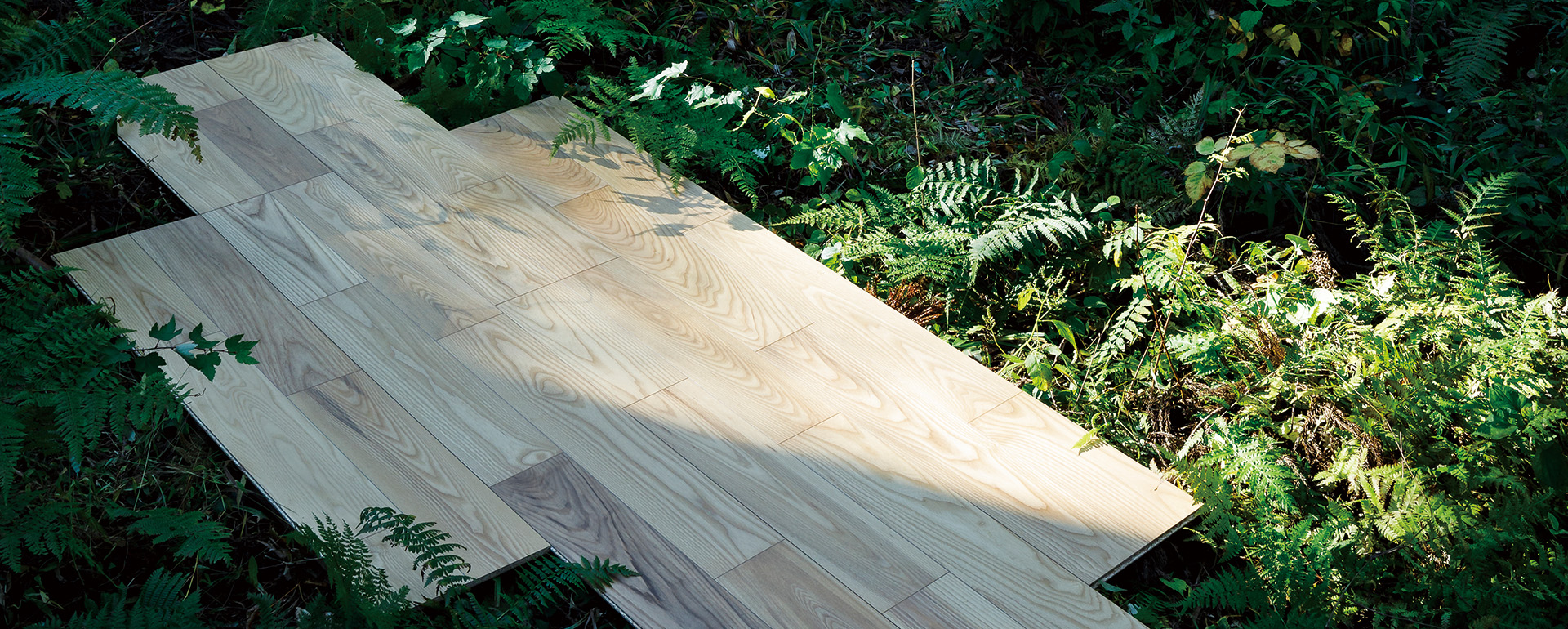
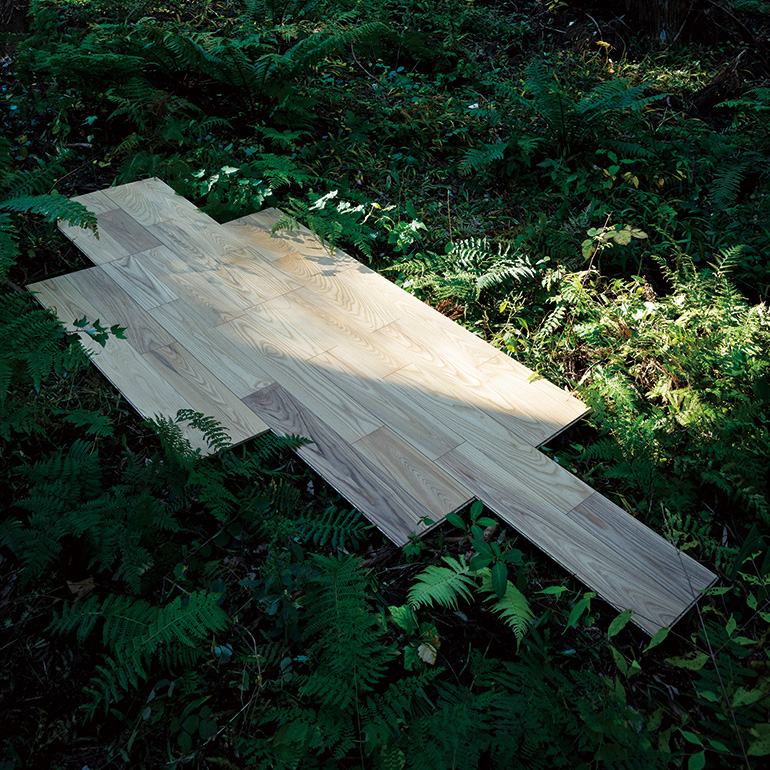
インタビュー│商品開発と製造担当者
テーマ
バイオマス塗料で従来品の高性能を担保する
塗料メーカーと協業し、バイオマスマークを取得した植物油脂由来の塗料を 業界に先立って、床材表面に採用。
環境にも配慮しながら、ダブルコートの性能で住む人の快適な生活を支えています。
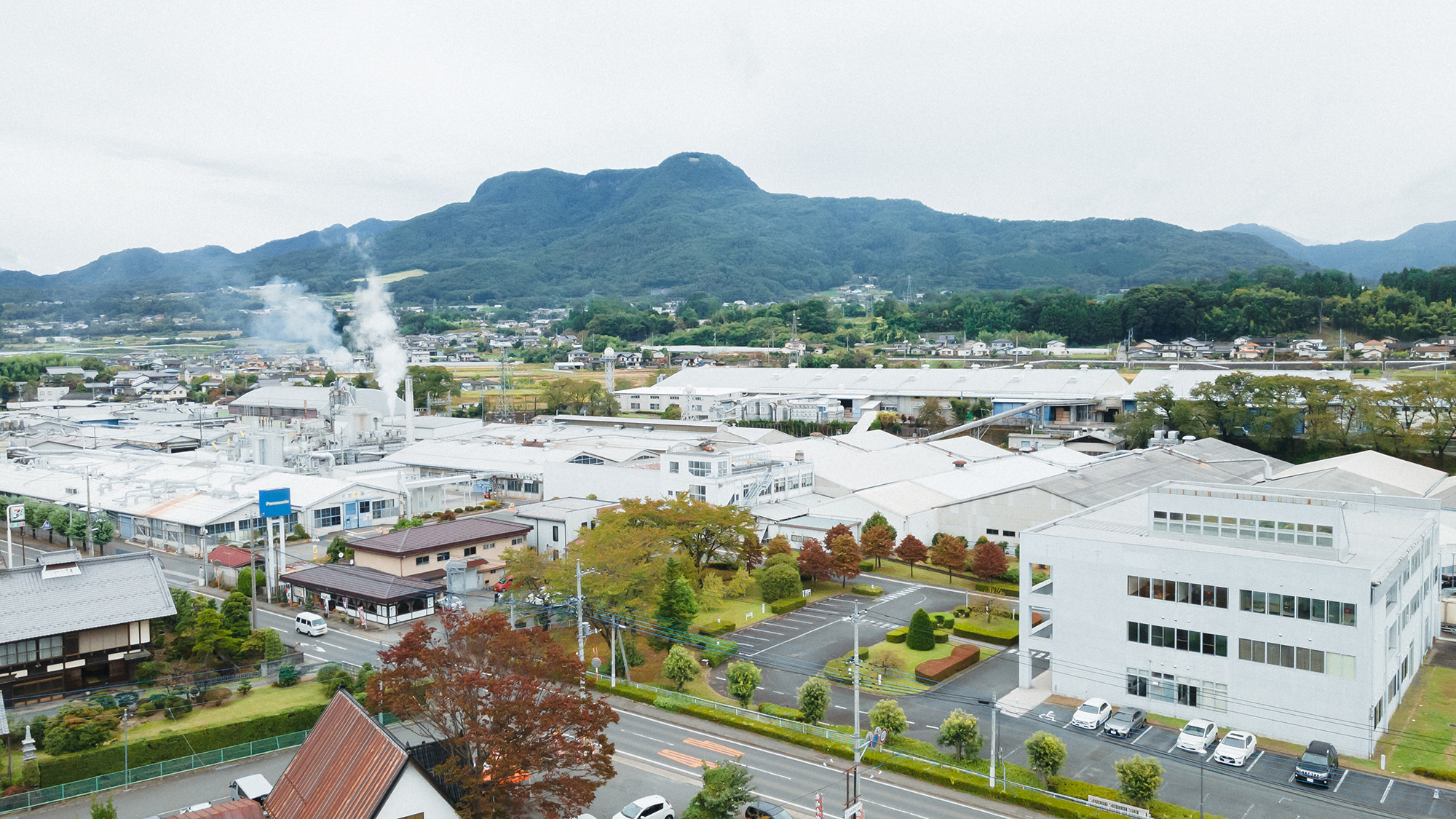
取材協力:パナソニック内装建材株式会社
【群馬工場】
群馬県沼田市井土上町135
https://panasonic.co.jp/phs/pibp/
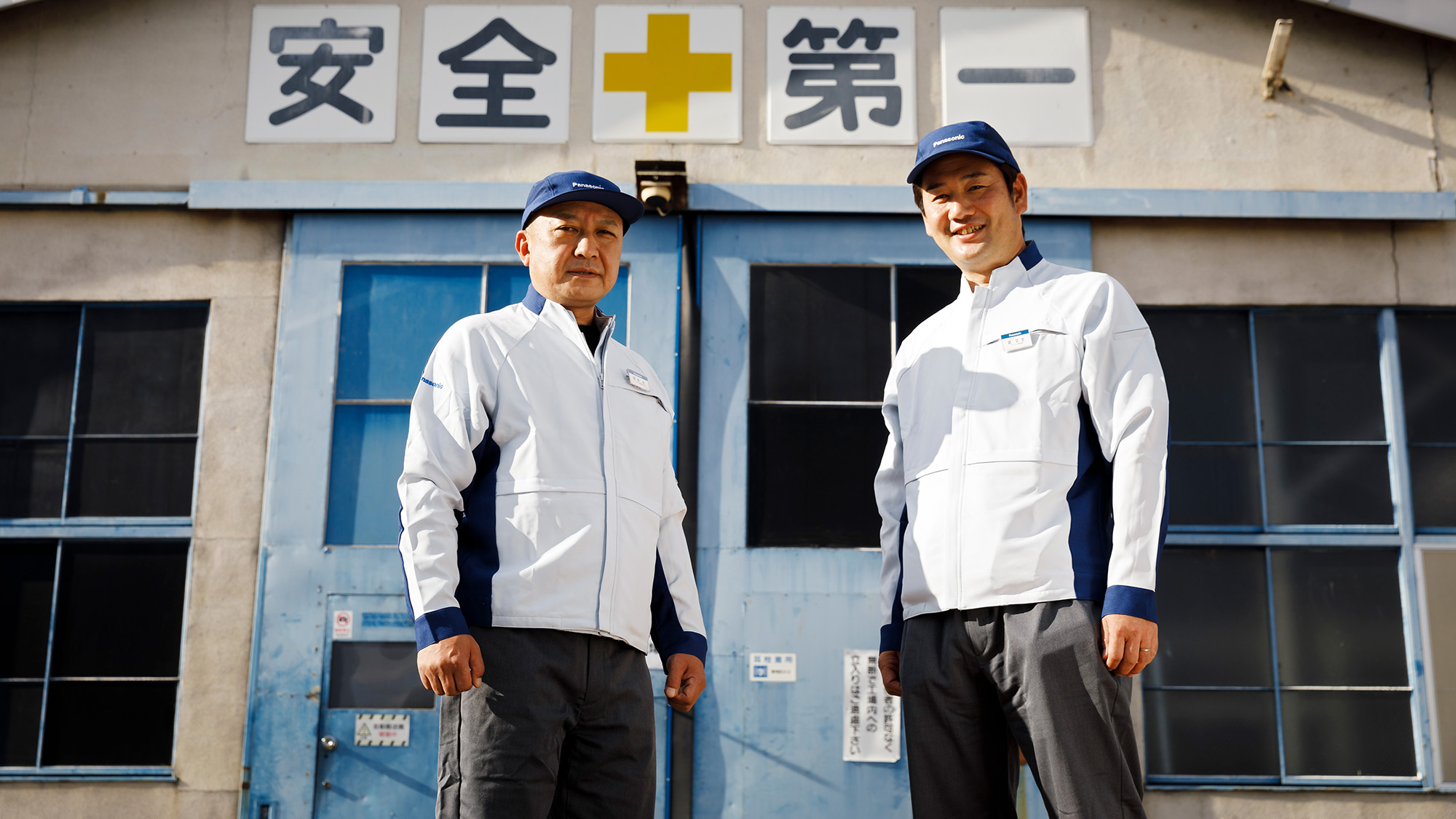
左:製造担当 飯森 武
右:開発担当 堤 文生
「チームワークの結集で着実に歩む」
環境配慮のバイオマス塗料を使用
取材者
サステナブルフロアー(以下、サステナブルフロアー)の企画を推進される中で、バイオマス塗料を採用しようということが決まったんですね?その経緯をお聞かせください。
堤
(開発担当)
環境への配慮が主流になっているいま、我々も床材で何かできないかと考えておりました。
そんな時、塗料メーカー様より植物由来の原料を使用したバイオマス塗料が商品として使用できるレベルになってきているという話を頂き、我々開発にとっては、環境配慮型の床材を商品化するまたとないチャンスだと思いました。
新塗料の採用にあたっては、床としての基本性能を維持しなければならないという問題がついて回ります。
特に今回は、従来の塗料と原料から異なるわけですから、床材の基本性能を担保できるのかというところが一番の課題でした。
開発段階でそれらの課題を確認し、解決していくためには、現場との密な連携が必須となります。
飯森職長にも多大なご協力を頂き、やり切ることができました。
今、それが商品として問題のないレベルで、環境配慮のバイオマス塗料を使用できる目処が立ち、量産化にむけて最終ステップに進むことができたということです。
強度に関する性能の大部分は塗装
取材者
取材者製造との連携という部分で、飯森職長が深く関わられたわけですね?
堤
堤はい。新塗料を採用する場合、はじめはラボなどで手作りレベルの試作から始めるのですが、最終的にはそれを製造ラインで量産しなければなりません。
ラボ段階が終了し次第、製造ラインでテストが始まります。
飯森職長には、テストの度に発生するトラブルや製造課題の解決にいろいろとご苦労いただきました。
取材者
取材者従来の化石燃料系の塗料でしたら、何十年にも渡る実績もありデータもしっかり取れていますが、それをバイオマス塗料に切り替えるということでご苦労されたところはありますか。
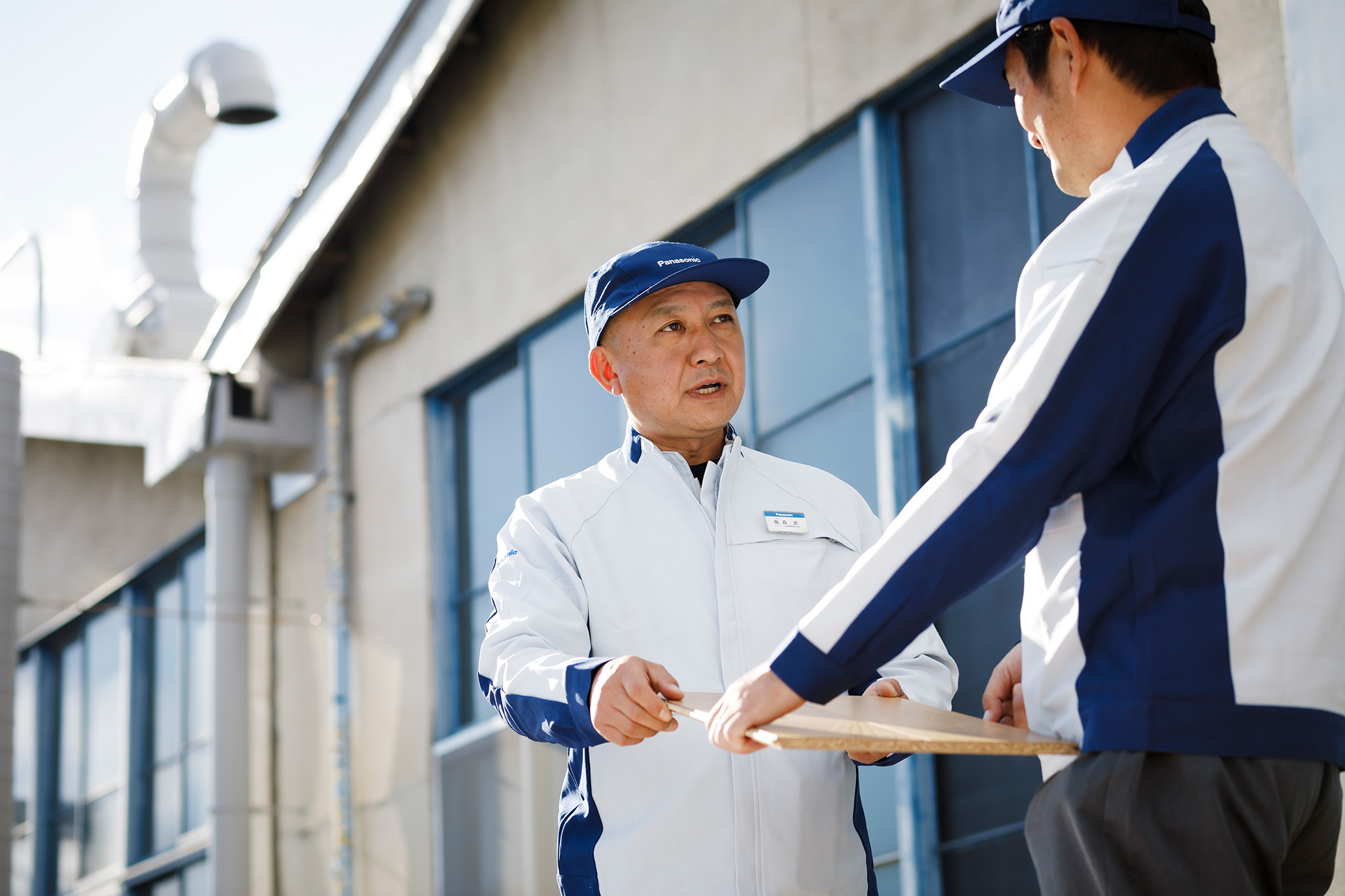
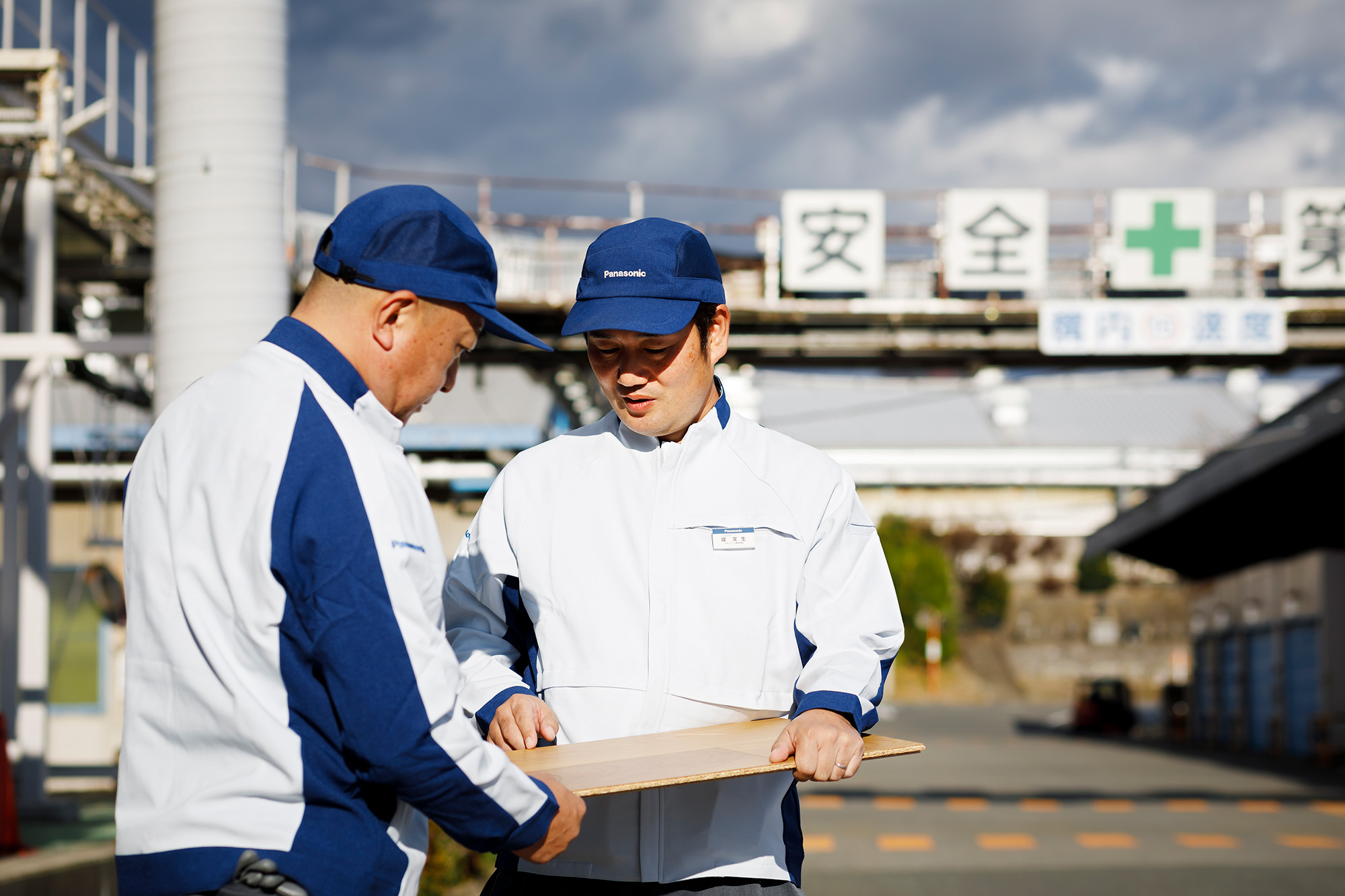
堤
堤一番はやはり性能面です。床ってただ敷いてあればいいというものではなくて、お客様が生活されるわけですから、椅子を引きずったり、重量物が置かれたり…とてもストレスがかかっています。
そんなストレスの影響をダイレクトにうけるのが表面の塗装部分であることから、強度に関する性能の大部分を塗装に頼ることになります。
ところが、はじめはなかなか目標の性能をクリアせず、塗料メーカー様と何度も相談しながら改良を重ねました。
それが今、ようやく現行商品と遜色のないところまで開発が進められ、製品としてお出しできるレベルに到達しました。
取材者
取材者開発期間はどの程度かかりましたか?
堤
堤企画構想から開発期間は8ヶ月ほどになります。
ちなみにバイオマス塗料を使用した床材は、業界では初めてではないかと思います。
取材者
取材者ユーザーにとっては、木材が硬い(強度がある)ということは直感的にイメージがわきますが、それに比べると表面塗装が重要だという意識はあまりないのでしょうか?
堤
堤ああ、そうかもしれませんね。
実際は、傷への強さに関して言うと表面塗装の方が支配的です。
逆に、重量物への強さ(凹みに対する強さ)となると基材の硬さが支配的になります。
そういった視点でみると、この商品はバイオマス塗料で傷への強さ、サステナブルボード基材で重量物への強さを保持しているわけです。
取材者
取材者表面塗装が変われば、お施主様のお手入れ方法も変わりますか?
堤
堤そこは変わりません。
表面塗装が変わったとしても、お客様が日常生活のお手入れが変わるわけではありませんので、現行商品と全く同じようにして頂ければ、快適に過ごして頂けます。
取材者
取材者サステナブルボード、いわゆるチップボード基材の話がでましたが、とても特殊な構造なんですね?
堤
堤はい、建築解体の際に出る廃材などをリサイクル材として粉砕し、固めて、床の基材として使えるように造られているのがサステナブルボードです。粉砕したチップを効率的かつ品質上支障がないように、少し粒子の細かいものを表面側にして、床材表面の平滑性を確保するなど工夫しております。
断面を見て頂けると確認できると思います。
梱包入り数を従来の6枚入りから、3枚入りに1本化
取材者
取材者ありがとうございます。
飯森職長からご覧になった堤さんの仕事ぶりはいかがでしたか?
飯森
(製造担当)
飯森(製造担当)製造ラインの現場担当からいいますと、製造ラインでトラブルやロスが少ない(歩留、工数、時間など)安定した生産ができる塗料にして欲しいというのが率直な思いでした。
開発途中で、製造課題だけでなく、表面性能が確保できない大きな課題もあり試行錯誤しましたが、最後まであきらめずに目標達成に向けて努力していた姿は今も忘れませんよね。
取材者
取材者サステナブルフロアーの梱包入り数を3枚入りにするために製造ラインの改造が必要だとお聞きしました。
飯森
飯森まさに今、形にするべく試行錯誤しており、これからラインの改造工事に取り掛かるという局面です。
今まで、床材を6枚入りで梱包していましたが、3枚入りの梱包も可能とするために設備の改造が必要でした。
必然的に従来と比べ2倍の梱包をしないといけないので、現状のままだとライン全体のサイクルが追いつかなくなります。
そのため、別の梱包機も同時に稼働させて同じ生産性を維持できるように推進しています。
取材者
取材者商品の仕様が変わるということは、製造現場としても大きな変化ですよね?
堤
堤生産方法の変化という視点では、この商品を造る場合、塗料をすべて切り替えなければいけません。となると、塗装設備に入っている従来の塗料を、一度全部抜き、洗浄し、新塗料を入れるということをしないと造れない。
ですから、この商品を生産するときには必ずそういう作業が製造現場で発生します。
取材者
取材者1回いっかい、機械を洗浄するということですか?
堤
堤そうですね、バイオマス塗料と他の塗料が混ざらないように管理するためにはそういった作業が必要となります。
しかし、塗料を切替るロスを極小化するために、次の改善に着手しはじめております。環境配慮商品ですから、有効資源をロスなく、ムダなく生産できることも、もちろん必要ですよね。
取材者
取材者ビジネスユーザー様の立場からすると、サステナブルボードの3枚梱包単位というのはできるだけ無駄を出さない、余りを出さないということにつながるわけですね?
堤
堤そうですね、いまは施工現場で1枚足りない場合、6枚発注しないといけないのですが、それが3枚の発注で済むということになります。
また、サステナブルボードの特性上、たくさんのチップを圧縮し固めていることから、通常の合板などと比較してどうしても重くなります。
ですから、1梱包中に6枚入り(32kg)とすると持ち運びがかなり重労働になります。これを、半分の3枚入り(16kg)にすることで、持ち運びの回数は増えますけれども、重量という点ではかなり楽になるのではないでしょうか。
バイオマスコートの技術を展開していくための大きな一歩
取材者
取材者環境配慮型の商品として一つの形ができました。さらにこの先の可能性、広がりみたいなものは・・・。
堤
堤今後、環境配慮という概念がさらに世の中に浸透するにつれ、床材だけでなく、他の内装材材にも展開されていくと思います。
また、技術の進歩に伴い、塗料のバイオマス度(使用しているバイオマス原料の割合)もますます高くなっていくでしょう。
今回一つの商品を確立できたことは、この後の商品へ技術を展開していくための大きな一歩となりました。
バイオマス塗装やサステナブルボードの技術は、今後の商品の主流になっていくのではないかと私は思っています。
取材者
取材者楽しみですね。
いろいろと積み上げてこられた企業文化を感じました。
堤
堤そうですね、一人でやれることには限りがあるので、チームワークの結集と言いますか、みんなで力を合わせて着実に歩んでまいります。
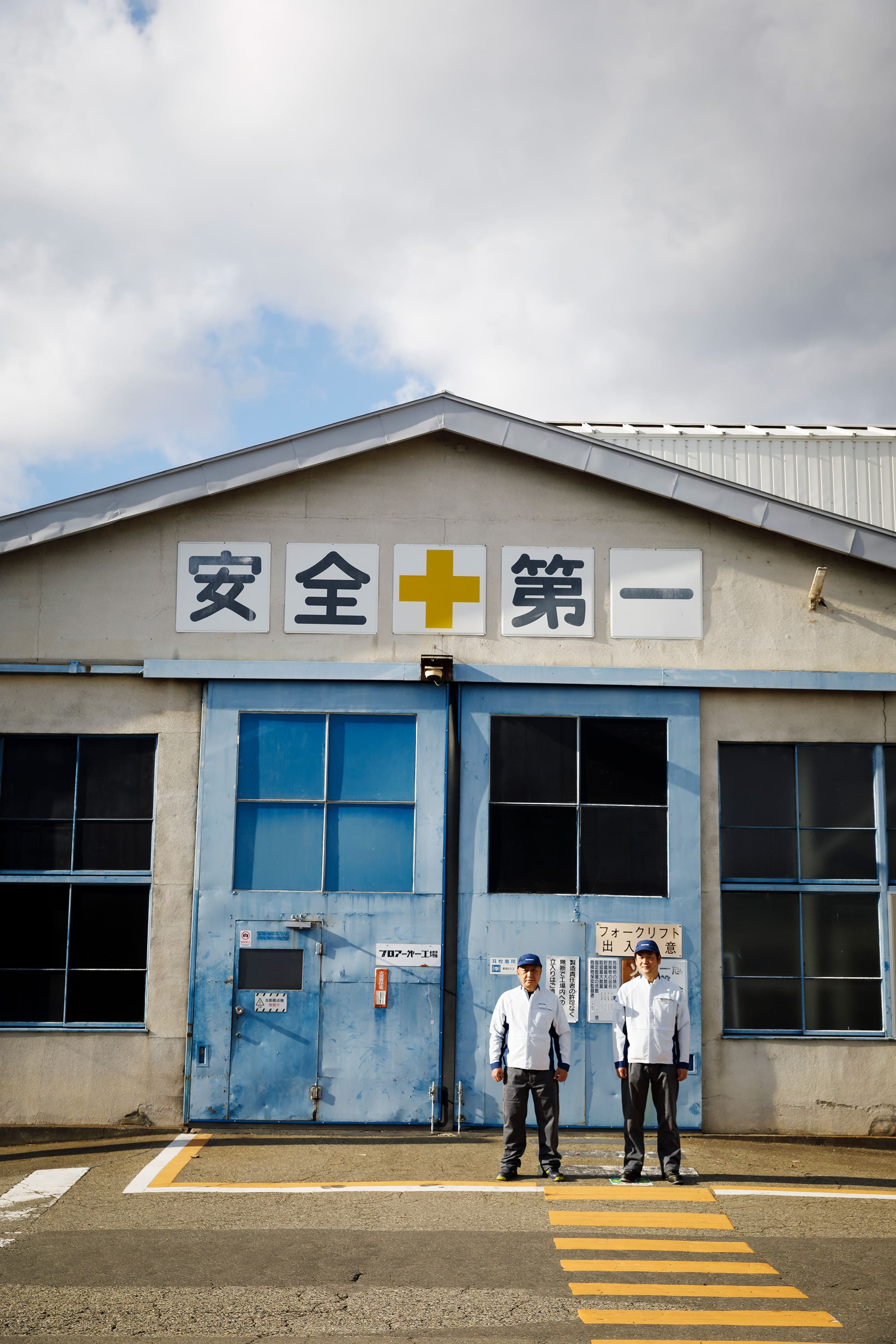
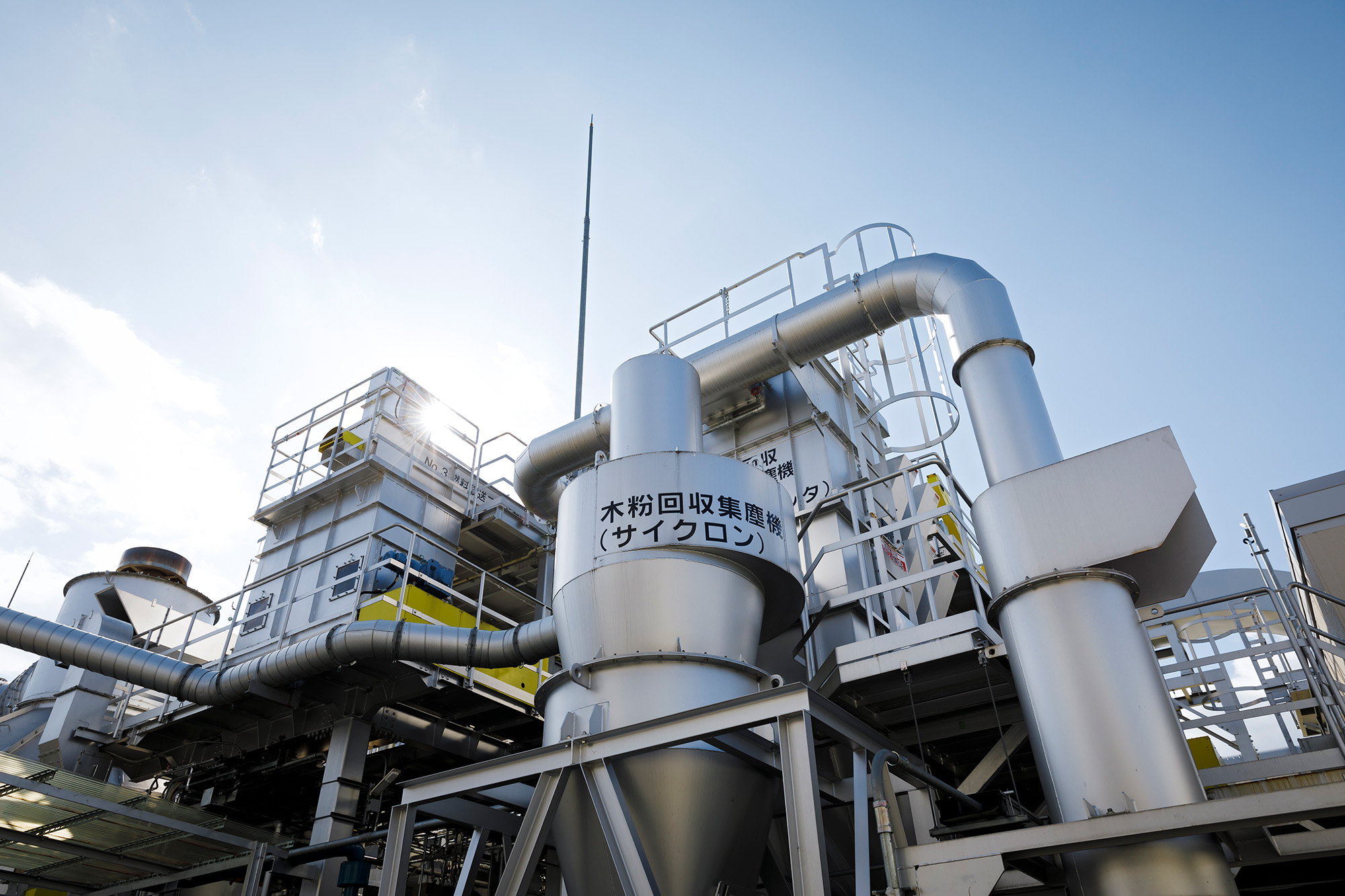
群馬工場のサーマルリサイクル施設
ビジネスのお客様
各種データのダウンロード
Panasonic製品のご提案にお役立てください